After the long natural formation process deep in the earth, the diamond is extracted from the mine in its rough, raw state, and begins on its next journey - to become a polished diamond.
From mine, to jewelry store, to the engagement ring finger of its eventual owner - every diamond undergoes a long and painstaking process of planning, cutting, polishing and grading. Over the past 30 years, computerization and digitization has penetrated the diamond production process. The use of technology has enabled far greater levels of precision, which, in turn, has impacted the diamond retail industry, enabling the development of special cuts and higher standards of diamond beauty.
Sarine, which is celebrating its 30th year in 2019, provides technologies along the entire diamond pipeline. For this reason, the company is in a unique position, having deep access at every stage of a diamond’s production. In celebration of our 30th year, and our comprehensive range of diamond production technologies, we’re going to take you on a journey along the road of diamond manufacturing, and explore how technology integrates with every stage:
Exploring the Diamond Production Process
Inclusion mapping
For diamond manufacturers, it is important to maximize the yield and quality of the polished diamond that can be cut from the rough. In order to make the best decision about how to cut the rough diamond, it first needs to undergo rough planning. The first stage of rough planning is inclusion mapping. The rough diamond is scanned by the Sarine Galaxy® device, which creates a precise image, or ‘map’, of the stone displaying comprehensive 3D visual information about its physical inclusions and flaws - their size, shape and location.
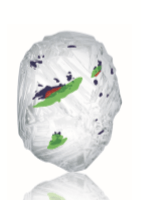
Planning
After inclusion mapping, it is time to create a cutting plan that will yield the best polished diamond or diamonds from the rough stone. This is carried out by software such as Sarine Advisor®, which uses the inclusion map of the rough diamond to ascertain the best position from which to extract the polished diamonds. The advantage of using software such as Advisor is its sheer capability to plan a multitude of different cutting options in a fraction of a second. In addition, the professional diamond planner can input specific filters and parameters (such as size, clarity, value and more) to create cutting plans whose output delivers the polished diamonds requested by the manufacturer’s clients. Accurate computerized planning enables maximum yield and profit of polished diamonds, in terms of both weight and quality, and increased efficiency in meeting customer demand.
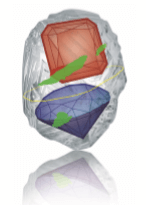
Sawing & Shaping
After the final cutting plan is decided upon, the next stage is sawing the rough diamond into segments, and shaping into a round, in preparation for the more refined polishing and finishing of the next stage. Sawing a rough diamond is not an easy task. It requires accurate cutting instructions and fine precision to ensure the diamond is not damaged or compromised. Even the smallest departure from the exact sawing line puts the diamond at risk of shattering or cracking. Sarine’s Quazer® is sawing technology that uses green laser to enable maximum accuracy while minimizing risk of damage to the rough diamond.
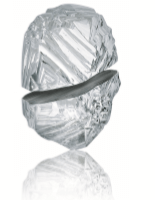
Polishing & Finishing
The polishing and finishing stage of diamond production demands the very highest level of attention and accuracy. Computerized software, such as Sarine’s Instructor®, enables the diamond cutter to measure and analyze the diamond throughout the polishing process to ensure adherence to the cutting plan. The use of advanced diamond scanning and computerized measurement and analysis supports a far greater precision than could be achieved with manual assessment.
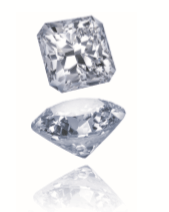
Laser Inscribing
Each polished diamond should be inscribed with an ID number that correlates with its lab report. Diamond inscriptions are not clearly visible to the naked eye. Personalized inscriptions, such as a love message or anniversary date, help to strengthen the buyer’s personal connection with the diamond. Sarine’s DiaScribe® diamond inscription technology is used in Sarine service centers and gem labs worldwide to accurately inscribe polished diamonds with verification and personal inscriptions.
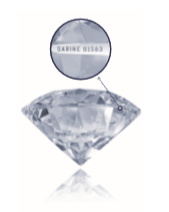
Grading & Imaging
The 4Cs grading system has been the industry standard for grading diamonds since the 1950s. Diamond scanning and measurement technologies, such as DiaMension® cut and symmetry grading, revolutionized the way that diamonds are graded, as they enable accurate standardization which cannot be achieved by the subjective perception of humans. More recently, artificial intelligence has been used to develop Sarine Clarity and Sarine Color technologies, which form the base for far more accurate and repeatable standards of color and clarity grading than have been used by the industry so far.
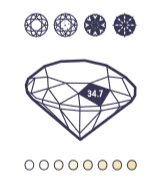
Diamond Report
The generation of a diamond report at a gemological lab is the final stage of producing a diamond for sale in the retail environment. The report offers a written record of the diamond’s gradings and features. It helps verify the diamond’s value and authenticity, and builds confidence during the sales process. Cross verified by the diamond’s ID inscription, the diamond report is an important component of the diamond’s overall position in the market. In recent years, Sarine Profile™ reports have created a new breakthrough in diamond grading and reporting, offering more than just technical diamond information. Sarine’s reports, produced at Sarine Technology Labs, are digital, interactive reports that include diamond imaging, expanded grading options such as light performance grading, and other diamond information, such as Hearts and Arrows imaging and more.
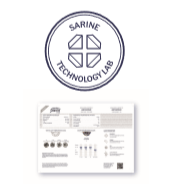
The journey a diamond takes from the mine to “it’s mine!” is long and complex, and it demands incredible skill, professional gemological knowledge, and access to high level technologies. As the technology becomes more sophisticated, the industry adapts, and new diamond experiences become available to consumers. Ultimately, the entire industry - from diamond manufacturer, to diamond seller, to diamond buyer - benefits.